Ich lerne CAD und 3D-Druck um ein NAS für Fotografen zu entwickeln
Die Krux mit den Daten
Als Fotograf ist mein wichtigstes Asset die Bilder, die ich über die letzten Jahre hinweg aufgenommen habe. Sie definieren wer ich bin und zeigen was ich kann. Diese Daten waren auf 10 Festplatten verteilt, wobei 5 die anderen 5 sicherten. Das war kompliziert, langsam, unübersichtlich, und ich konnte nicht einmal remote darauf zugreifen. Offen gesagt war es auch dumm, weil mir durch dieses komplizierte Handling auch Fehler unterlaufen sind, was zu Datenverlust führte.
Unter anderem liebe ich die Option, spontan auf Bilder zugreifen zu können um mit Photoshop zu spielen, was so nicht möglich war. Früher hatte ich zwar NAS-Systeme von QNAP oder Synology, womit genau das funktionierte, zufrieden war ich aber nicht. Sie waren laut, langsam und unflexibel. Besonders störte mich die Lautstärke: nicht entkoppelte Festplatten und laute Industrielüfter bereiteten mir Kopfschmerzen.
Custom-Systeme (Computer, Rad, Golf) maßgeschneidert auf die Bedürfnisse des Anwenders haben mich schon immer interessiert und nach etwas Recherche habe ich festgestellt, dass es gar nicht so aufwändig ist, sich selbst so ein NAS, zum Speichern der Daten, zu bauen. Die Software für die ich mich entschieden habe ist Unraid, für meinen Usecase das beste Produkt. Eine Lizenz für 6 Platten liegt bei $ 49,00, inklusive kostenloser Updates für ein Jahr.
Aus alten und einigen neuen Komponenten habe ich mir ein passendes System gebaut, Unraid installiert und schon ging es los. Alles perfekt! Fast …
Das erste eigene NAS
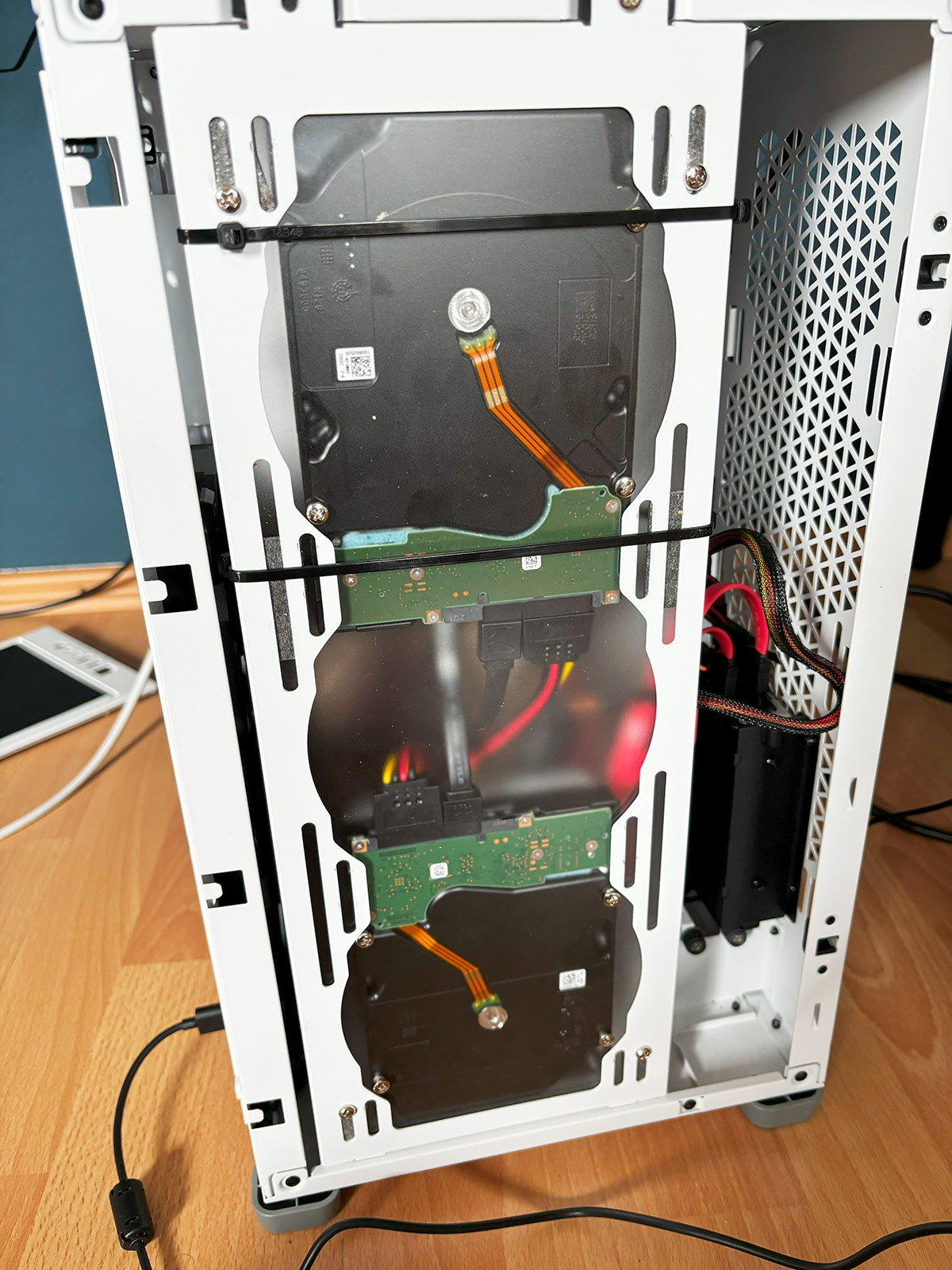
Mein altes Corsair Mini-ITX Gehäuse hatte keinen Platz vorgesehen für 3,5" & 2,5" Festplatten, also hatte ich die Schiene, an der sich normal ein Radiator befindet, zu einem Festplattenhalter umfunktioniert. Etwas Acryl und ein paar Kabelbinder wirkten Wunder. Im Hintergrund ist ein Käfig für 2,5" Platten, den ich am Gehäuse festgeschraubt habe.
Das funktionierte hervorragend, allerdings sah es auch wirklich scheiße aus, noch dazu war die Kiste laut, da die Vibrationen der Platten auf das Gehäuse übertragen wurden. Auch ein Upgrade auf weitere Platten war hier quasi nicht mehr möglich, dafür ist kein Platz da. Zusätzlich war das Gehäuse relativ groß, bemessen an dem, was es eigentlich könnte.
Trotzdem hat sich der Designer in mir berufen gefühlt, dies zu ändern und aus meinem alten Gehäuse das bestmögliche herauszuholen.
Optimierungsversuche mit einem 3D-Drucker
Um meine Bestrebungen etwas zu professionalisieren, kaufte ich einen Bambu Lab A1 mit AMS-System, zum Drucken von weiteren Filamenten. Zu diesem Zeitpunkt hatte ich wirklich noch gar keine Ahnung von Druckern und habe mich blind auf ein paar Google-Rezensionen verlassen - womit ich zum Glück richtig lag. Die Installation des Druckers war einfach, auspacken, Transportsicherungen lösen, Filament (auch das war neu für mich) laden und schon konnte es los gehen.
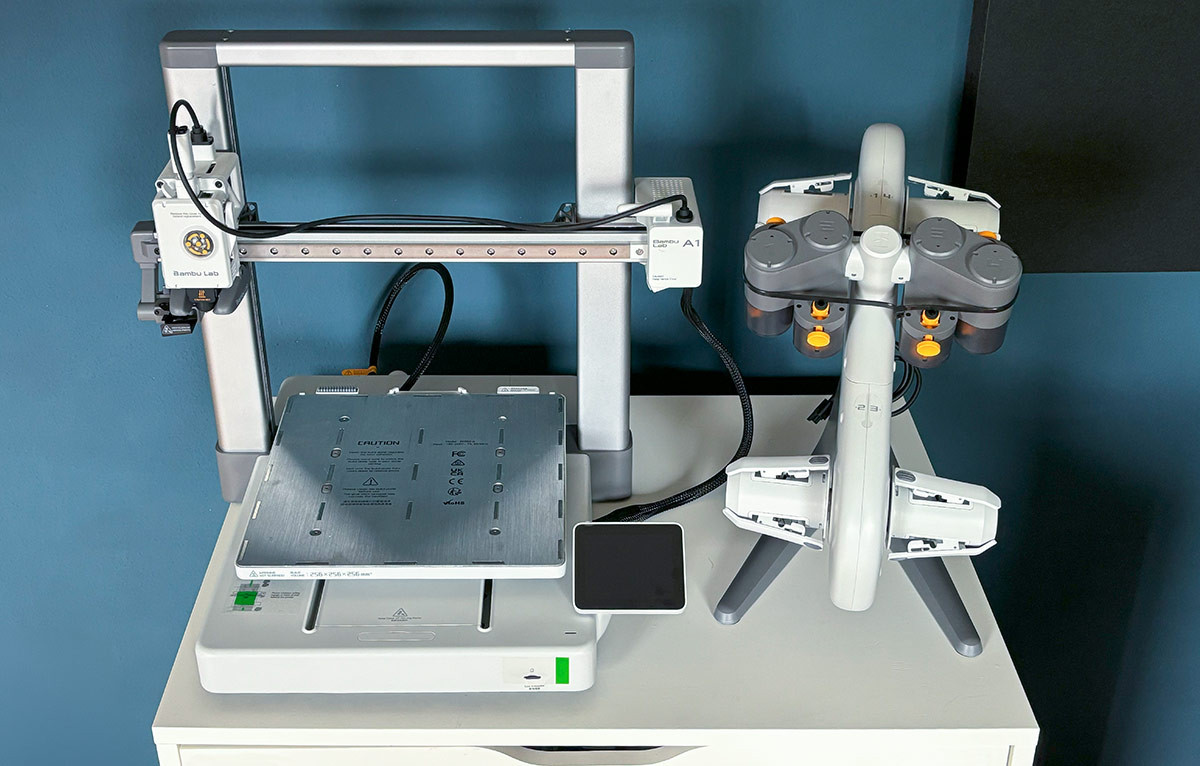
Wovon ich auch keine Ahnung hatte? Wie erstelle ich eigentlich ein Modell, von allem was ich so drucken will?
Groß testen und ausprobieren war noch nie mein Ding. Ich bin ehrlich, Kaufentscheidungen treffe ich meistens anhand des Etiketts. Mir muss es eben gefallen. Wieso fotografiert man sonst mit Leica?
Ich habe ein Advertisement für Shapr3D, eine CAD Software für Prototyping gesehen, die Demo geladen und bin dabei geblieben. Profis nutzen wohl eher Solid Works oder Autodesk Fusion. Im Moment macht Shapr aber für mich genau was es soll und es war/ist einfach zu lernen, da alles sehr visuell aufgebaut ist.
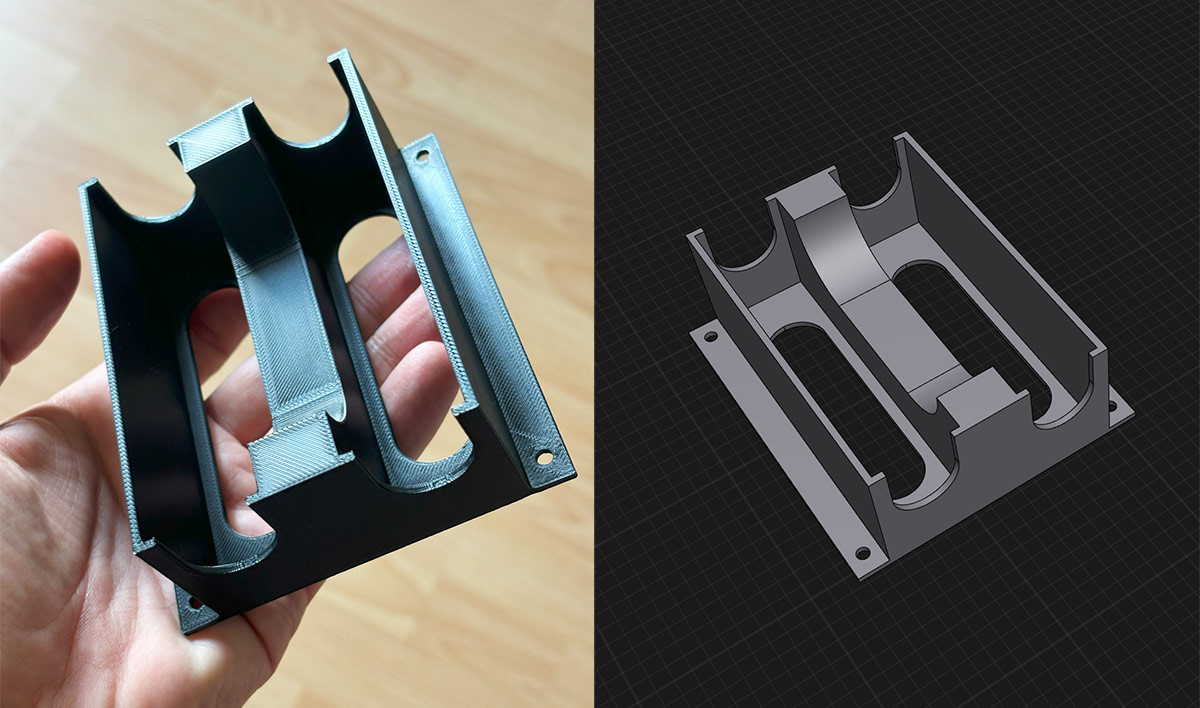
Nach kurzer Einarbeitung in die Software, ging es dann auch direkt los mit meinem ersten Modell. Einer Halterung für zwei Festplatten, die man am Boden des Gehäuses verschrauben kann. Auch das funktioniert hervorragend, schön ist es aber nicht.
Ab diesem Punkt fühlte ich mich wieder einmal berufen. Warum nicht gleich ein komplettes Case bauen? Kompakter, leiser, effektiver?
Ein eigenes Gehäuse entwickeln und drucken
Voller Stolz präsentiere ich das erste Ergebnis meiner Entwicklungen:
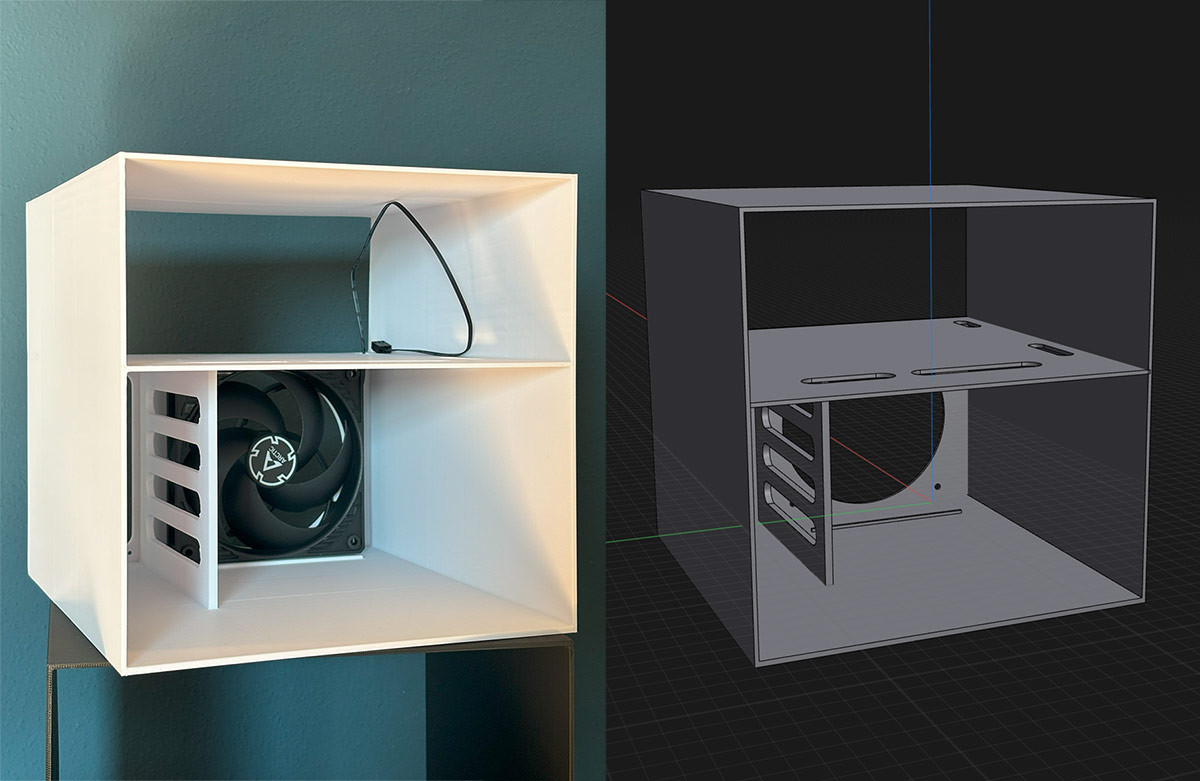
Schrott in einem Guss, aus 650 Gramm Filament, mit 13 Stunden Druckzeit!
Was für eine dumme Idee, alles in einem Rutsch zu drucken. 3D Druck ist nie 100% Präzise, Toleranzen müssen eingerechnet werden. Je umfangreicher der Druck, desto mehr kann schief laufen. In meinem Fall hat das Netzteil nicht 100% in den vorgesehenen Slot gepasst, also war mein Druck unbrauchbar (so richtig schön ist das Modell ja jetzt auch nicht).
Ich lerne dazu

Mir ist schnell klar geworden, dass es schlauer ist, mein NAS aus Einzelteilen zu konstruieren, damit ich flexibel Anpassungen und Designänderungen vornehmen kann. Also habe ich mich erst einmal damit beschäftigt, ein System zu entwickeln mit dem ich Komponenten ineinander stecken kann und was dabei gleichzeitig stabil bleibt.
Dabei habe ich eine ganze Menge über das Material gelernt und wie ich die Toleranzen entsprechend anpassen muss, damit die Komponenten ineinander greifen.
Basierend auf meinen Learnings habe ich die Einzelkomponenten des Systems konstruiert. Eine Fassung für einen 120mm Lüfter, der die Festplatten kühlen soll. Ein Gehäuse für das Netzteil inkl. eines Bereiches, in dem die Kabel lagern. Den Käfig inkl. Fassung für die 6 Festplatten und den Tray, auf dem das Mainboard aufliegt.
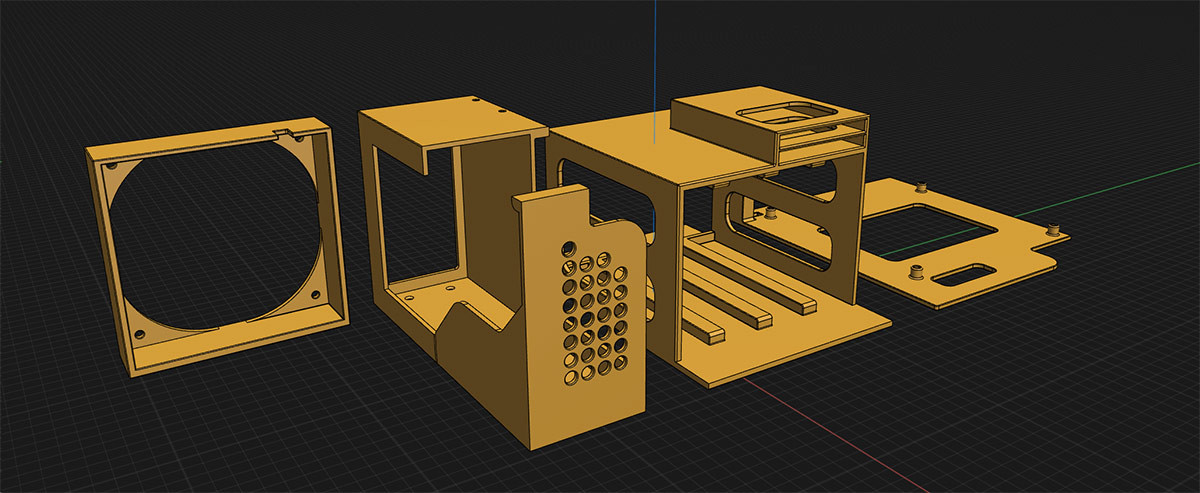
Das Finale Gehäuse
Nachdem ich die tragenden Teile des Gehäuses inkl. Boden und Deckel konstruiert hatte ergab sich ein Gesamtbild des NAS.
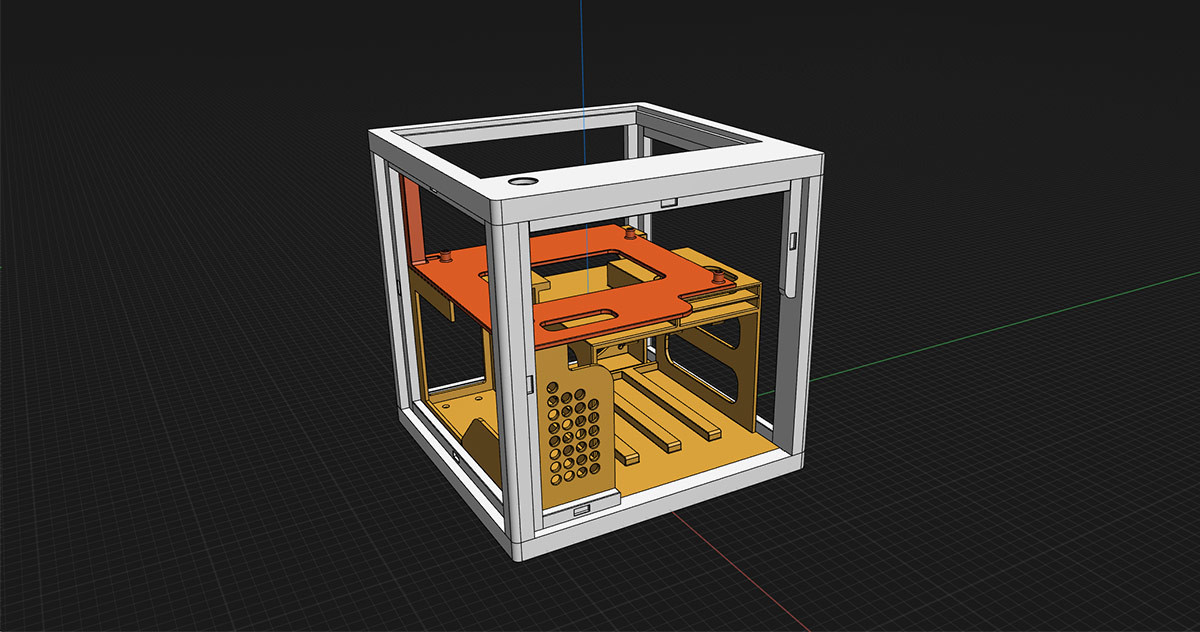
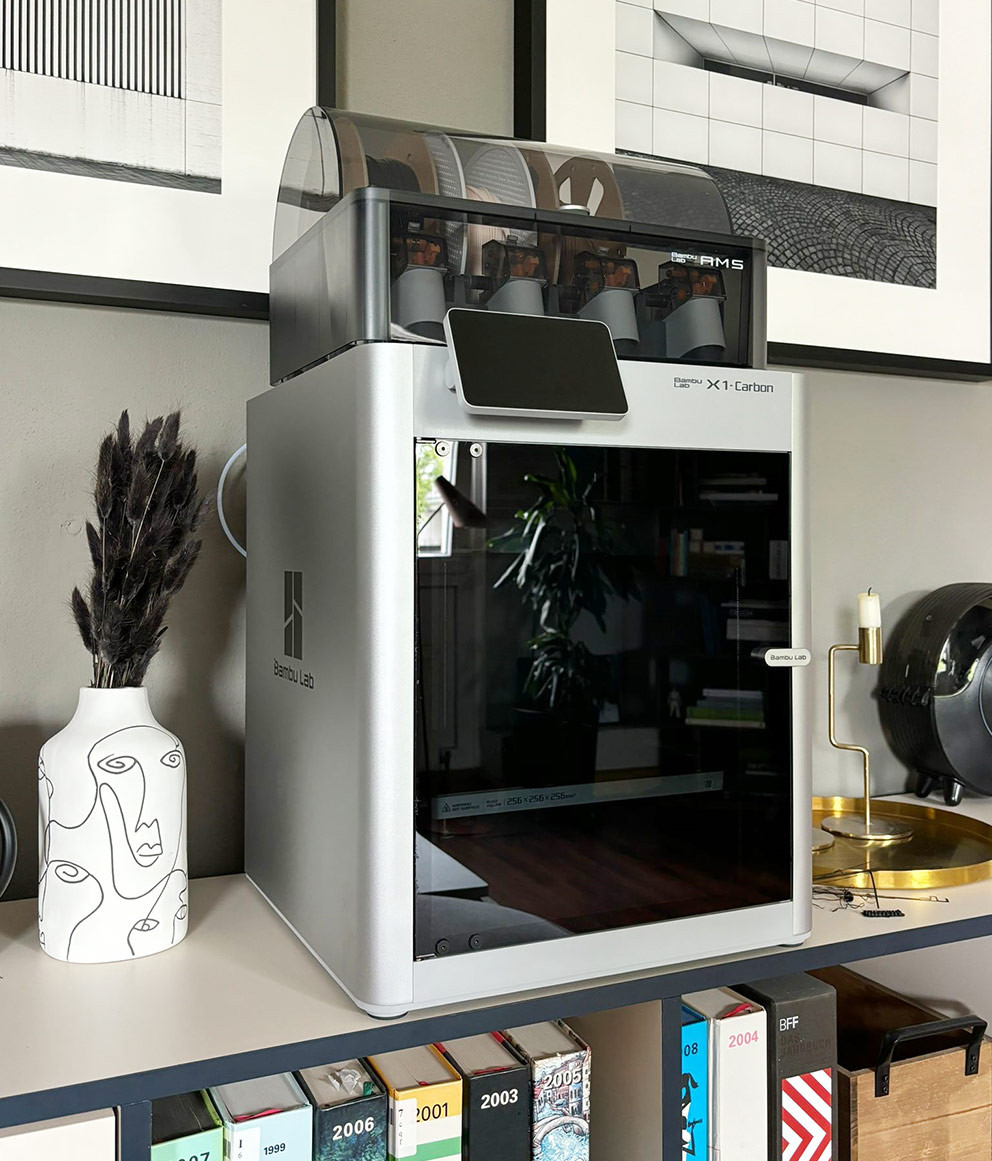
Zur Verstärkung meiner exzessiven 3D-Druck Tests habe ich mir mittlerweile einen zweiten Drucker zugelegt. Den X1C, ebenfalls von Bambu Lab.
Filament reagiert empfindlich auf Luftströme. Offene Fenster, Bewegungen im Raum oder Ähnliches beschädigen einen laufenden Druck sehr schnell. Dabei kühlen einzelne Schichten des Drucks schneller aus als andere und verändern dabei die Statik. Es bildet sich ein Warping, der Druck verzieht sich an den Ecken. Ich habe leider keinen Keller in dem dem der Drucker ungestört vor sich hinruckeln kann. Bei mir ist es im Sommer warm, alle Fenster sind offen.
Daher wollte ich einen Drucker mit einem geschlossenen Gehäuse, damit genau so etwas nicht passieren kann. Zusätzlich ist das Filament mit einer eigenen Box hier besonders gut vor Feuchtigkeit geschützt - und eigentlich sieht er auch ganz hübsch aus, wenn ich ehrlich bin - sagt sogar die Freundin, ich darf ihn erst mal im Wohnzimmer stehen lassen.
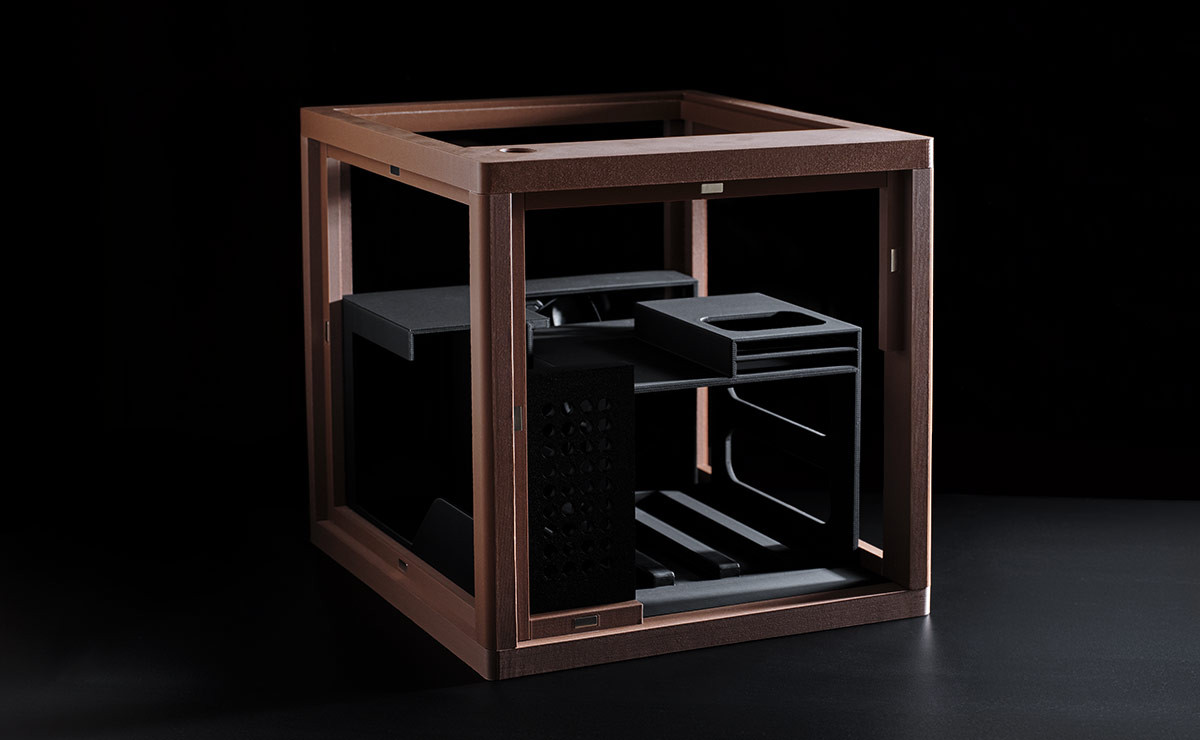
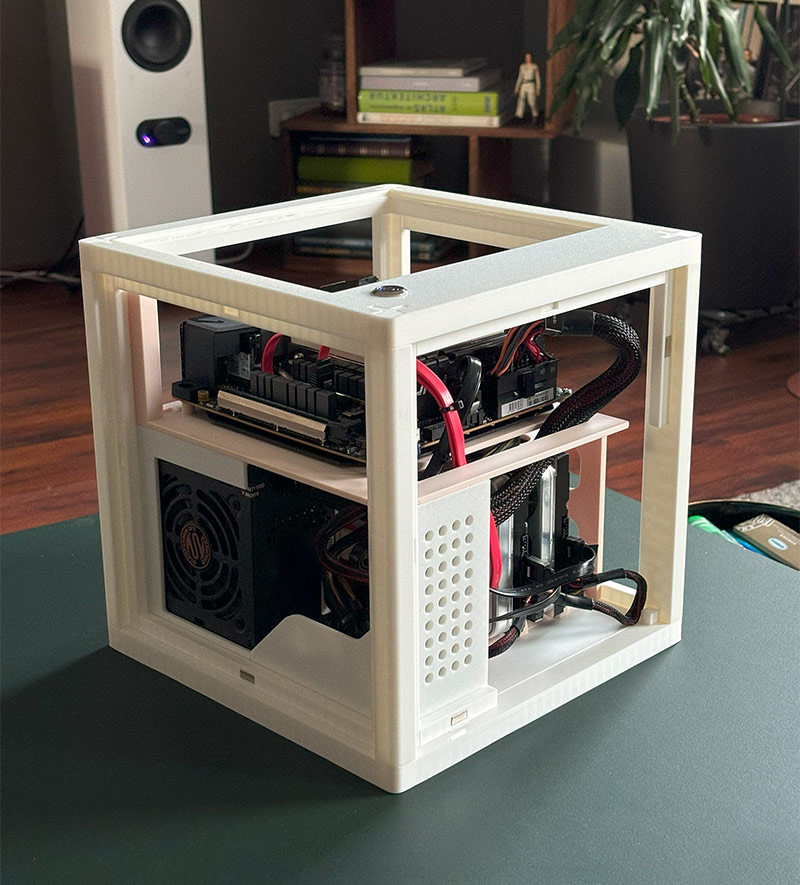
Oben zu sehen:
Aufnahme des fast fertigen Gehäuses. Lediglich der Mainboard Tray und die Seitenteile fehlen noch.
Links zu sehen:
Die Testversion des Gehäuses in dünnwandigem Druck um den Einbau der Komponenten zu testen. Hier ist bereits die komplette Hardware verbaut.
Die Festplatten und das Netzteil müssen nicht verschraubt werden. Beides wird einfach eingeschoben und hält stabil. Die Platten sind mit Schaumstoff vom Gehäuse entkoppelt.
Hier jetzt einige Bilder des fertigen NAS, an seinem Verwendungsort.
Das Schöne am 3D-Druck ist, dass so gut wie alle Farben erhältlich sind, so können unendlich viele Kombinationen ausprobiert werden. Sogar Transparent ist möglich. Ich finde mein Gehäuse verschmilzt (dafür was es ist) sehr unauffällig in den Hintergrund. Ist es schon perfekt? Sicherlich nicht. Die nächste Version möchte ich noch flexibler gestalten, was den Aufbau angeht. Auch eine Version für 6 x 3,5" HDDs würde ich gerne angehen.
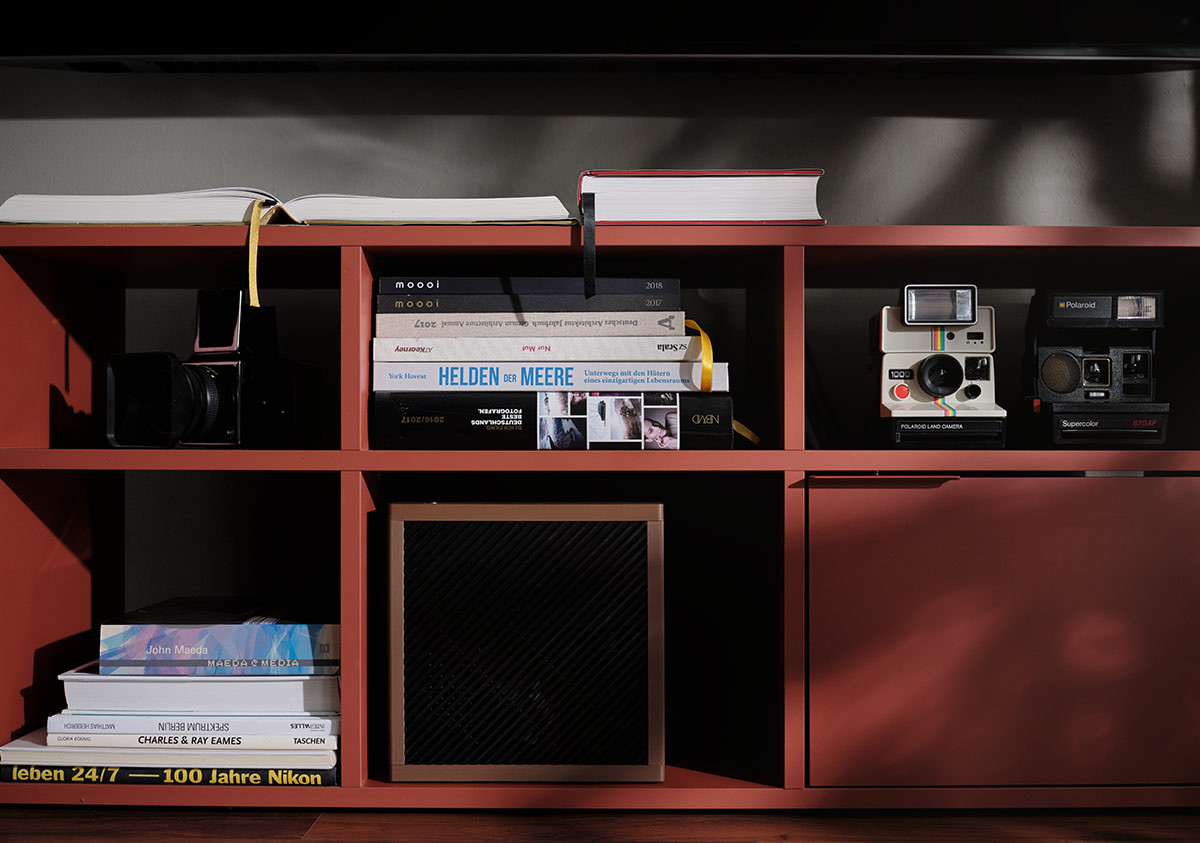
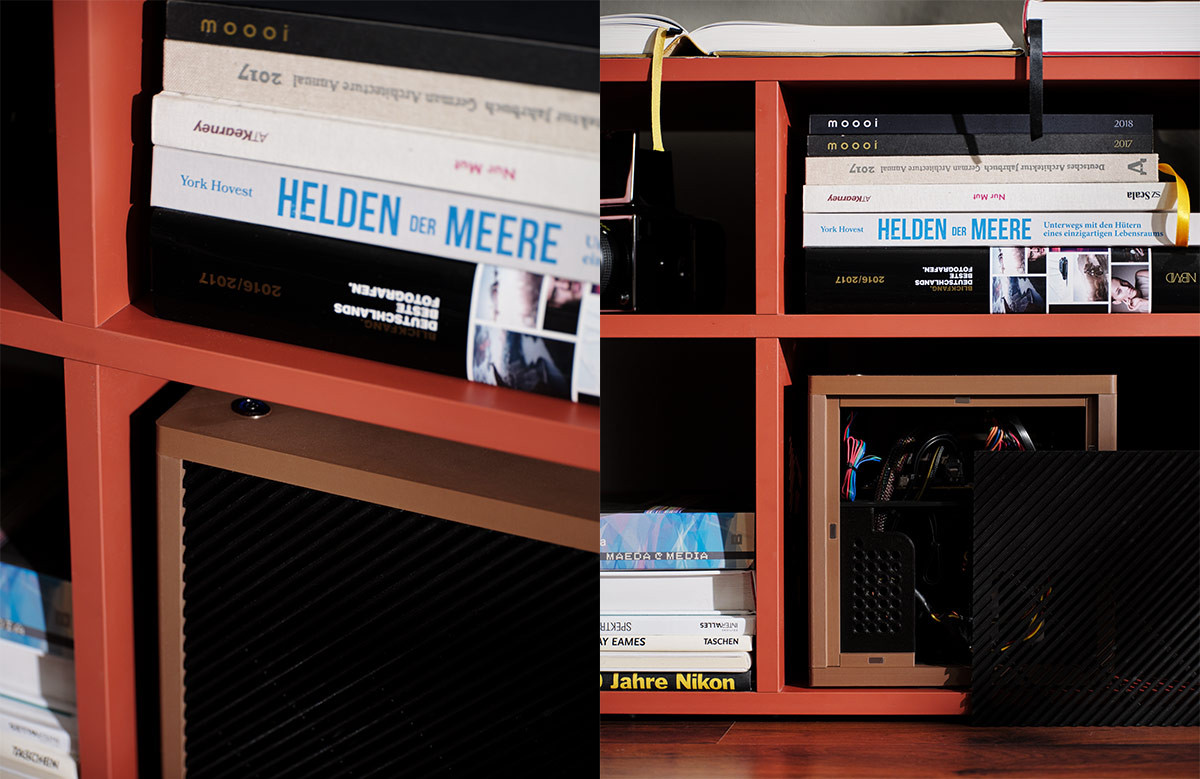

Facts
Konzipiert für Mini-ITX Mainboards und SFX Netzteile
4x 3,5" HDD (entkoppelt) Slots
2x 2,5" SSD Slots
120mm Low-Noise Fan für Festplatten
25 x 25 x 25 cm
Magnetische Seitenteile
10 Gbit möglich
Ca 900 gr. Filament
Die Druckzeit liegt alles in allem bei ca. 26 Stunden für die einzelnen Teile, unterscheidet sich aber je nach verwendetem 3D Drucker.
Ich muss sagen, ich habe etwas die Nadel im Arm. 3D-Druck und das Gestalten in der Software macht mir unglaublich viel Spaß. Es ist toll ein tatsächliches Produkt in seinen Händen halten zu können.
Stay tuned - ich werde sicherlich noch mehr drucken und im Besonderen an der nächsten Version dieses Gehäuses arbeiten. Kommentare oder Lust dich über 3D-Druck zu unterhalten? Melde dich gerne bei mir.